High quality cubical aggregate product
After remaining inactive since late 2007, Lafarge North America has reopened its Town of Niagara Quarry located in western New York. Lafarge had closed the quarry, which produces crushed stone primarily used in the region’s road projects, due to the weakened economic climate. The Niagara Quarry’s dolomitic limestone formation is a feature of the overall Niagara Escarpment geology.
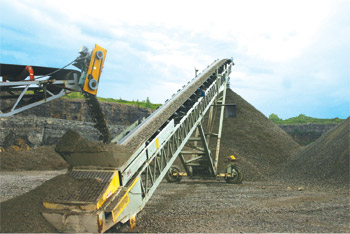
Perry Galdenzi, commercial manager — Aggregates/Asphalt for Lafarge North America’s Eastern U.S. Region sheds some light on the area’s history. Niagara Quarry, once known as Redland Niagara, owned by Redland Quarries Inc., was acquired by Lafarge back in 1997. Lafarge Group today is recognized as the world’s leader in building materials — cement, concrete, aggregates and gypsum. Lafarge North America has several local operations in Western NY, including a cement crusher terminal in Buffalo and an asphalt plant in Lockport employing some 181 area workers. Lockport, just 12 miles east of Niagara, was originally opened in the 1950’s and produces 1,500 tons per hour of material, roughly two million tons per year. So when the recession hit in 2007, Lockport alone provided ample capacity to keep up with the needs of area construction projects.
Positive news for customers, company revenues and employment came in spring of this year, when Lafarge management anticipated a pick up in the economy, and the search began for the right contract crushing firm with the most reliable, efficient two stage crushing system to get aggregate production up and running again at the site. By May, crushing resumed to fill increased material demands, and the Niagara Quarry is currently operating six days a week.
“We previously ran our own Cedar Rapids impact crushing installation at this site. It was somewhat piecemeal and maintenance was a constant issue” states Lafarge’s Galdenzi. This time we decided to employ contract crushing and selected Catco Crushing out of Alden, NY to handle the project.” Catco’s state of the art Lippmann two stage crushing and screening plant consists of a robust Lippmann 3062 Portable Primary Jaw Plant teamed with a Lippmann 5165 Portable Secondary Impact Crushing Plant. The crushing circuit is currently producing 1-3/4-inch crusher run road base at 500 to 600 tph” says Galdenzi. “We eventually expect 200,000 to 300,000 tons from this plant and we have reserves for the next 25 to 30 years” Perry continues.
Catco (Concrete Applied Technologies Corporation), one of the major road builders in western NY, is owned by Mike Salvadore, a civil engineer licensed in the state of New York. Mike started the company in 1995 with 20 employees and revenues of around $3 million. Determined, unafraid of hard work and one who believes in accountability, Mike’s respected highway and heavy construction company is an American success story, as today he’s grown his firm into an operation with 140 employees and $40 million in annual revenues, largely serving the NY state DOT, the local cities of Niagara Falls and Buffalo and area counties. Lafarge has enjoyed a strong relationship with Catco and has been a major Catco material supplier for many years.
While Catco’s Lippmann two stage plant is highly efficient at crushing virgin limestone at the Niagara Quarry, Salvadore purchased the system for future large scale contract recycling jobs. “More than anyone in upstate NY, we have been committed to recycling” states Salvadore. “At some point we plan to have the largest recycle yard in Western NY” he claims.
Averaging 500-600 tph, Lippmann's 3062 Primary Jaw Plant teams well with Lippmann’s 5165 Secondary Impact Crushing and Screening Plant in this productive two stage aggregate crushing application.
Lippmann 3062 Primary Jaw Crushing Plant is ideal for high capacity aggregate and concrete recycle applications.
Mike points out some features on the Lippmann equipment. “Unlike other makes of recycle plants, the Lippmann 3062 Jaw Plant has higher clearance room under the jaw and employs a 60-inch x 30-foot recycle side discharge conveyor under the crusher complete with pan vibrating feeder.
An inline 55-inch Dings magnet removes rebar and other uncrushables. No small issue as this eliminates common hang ups with rebar at transfer points, and the consequent downtime that can be encountered with other crushing plants. Because we crush some 150,000 tons of recycled concrete per year on our own projects alone, a 30,000 ton pile of scrap rebar is not unusual for us” Mike states.
Catco investigated some track mounted crushing units, due to ease of portability, but because of the volume and tonnage Catco anticipates processing, the serious throughput that Lippmann’s 3062 Jaw provides was a better match for the company’s requirements, Mike explains.
Mike has always had a passion for the aggregate production side of the highway and heavy construction business. And when due diligence time came to select the right brand for their first crushing plant, Mike turned to Joe Sidonio of Upstate Screens and Crushers located in Holley, NY, Lippmann’s area representative.
Joe had previously sold Catco screens and other equipment and Mike’s first crushing plant purchase was a Lippmann 4800 Portable Impact Recycle Crushing Plant. Success with that machine, Mike’s experience with Joe’s company and Lippmann’s factory support convinced Catco to later upgrade to a larger Lippmann two stage concrete recycle crushing system.
Mike indicates his construction company presently owns some 70 pieces of CAT iron. “My CAT dealer tried to sell me Metso crushing equipment, but while I love CAT, when it comes to crushers, I trust Lippmann. Lippmann has phenomenal support. I had to go where you can be with people you can depend on and trust — day in and day out. Crushing equipment is just too big of an investment, too specialized. I spent a lot of time with Joe Sidonio and Bob Turner, Lippmann’s president at ConExpo. Joe showed me a Lippmann plant operating in Rochester, NY and I was impressed. I rented one a year or two later and was entirely convinced. Lippmann stands behind their equipment. Joe is out here making certain everything is operating optimally. Anyone can occasionally have problems, but it’s how problems get handled that’s critical in our business” Mike emphasizes.
Catco’s 3062 Lippmann Jaw Plant features convenient options like a hydraulic toggle which saves countless hours and allows the setting to be adjusted while crushing. The heart of the plant, a heavy duty recycle Jaw featuring a reliable rugged frame with ribbed steel plate construction, an oversized heat treated forged shaft and radial thrust tapered roller bearings, offers a huge 30-inch x 62-inch feed opening that accepts massive slabs of concrete full of rebar, reducing feed time and wear costs and designed to achieve maximum capacity. Reversible jaw dies assure maximum wear life. Mounted on a robust chassis with a travel height of 13-foot 6-inches, the plant is designed for easy set up and tear down, has a 62-inch x 20-foot vibrating grizzly feeder and hydraulic leveling legs.
The Jaw Plant is teamed with Lippmann’s 5165 Secondary Impact Crushing Plant featuring hydraulic curtain adjustment, a 6-foot x 20-footdouble deck screen, pan feeder, jacking legs, jib crane and cross conveyor for making multiple products.
A rock box from the previous installation feeds the Lippmann 3062 Jaw Plant’s 62-inch x 20-foot heavy duty vibrating grizzly feeder. The Jaw's huge 30-inch x 62-inch feed opening accepts large rock fractions reducing material preparation costs.
This Lippmann 5165 Secondary Impact Crushing Plant features hydraulic adjustment, a 6-inch x 20-inch double deck screen, pan feeder, jacking legs, jib crane and cross conveyor for making multiple products.
At the Lafarge installation, shot rock is loaded into CAT 730 haul trucks by a CAT 345B excavator. Dump trucks ramp up to a rock box which feeds the Lippmann Jaw Crusher Plant’s 62-inch x 20-foot flared type heavy duty vibrating grizzly feeder with AR steel liners and Hardox 400 hopper. The plant’s feeder is supported by heavy duty reinforcing ribs. The side discharge conveyor is sized to match the feeder and crusher capacities.
The drive choice for this plant was an electric power unit and variable speed drive for both the discharge conveyor and feeder. Key to the installation on the crushing site has been Bob Lewczyk, Catco’s equipment manager. Bob is in charge of Catco’s staff of mechanics at the company’s large, modern maintenance and service facility. Bob cut apart the old existing plant, organized conveying systems, electrical, pumping and redirecting water and other logistics.
Joe Sidonio explains that once Catco had the Lafarge contract in hand, Lippmann built the Jaw within four weeks, followed by the arrival of the self-contained Lippmann 5165 Impact Crushing and Screening Plant. The Jaw was assembled in one day and put in position using the existing rock box on site from the previous plant and employing the needed cribbing.
Mike indicates the Lippmann spread will remain at the Niagara Quarry Crusher the entire year and may process material there for some extended time. They will use their original Lippmann 4800 Impactor Plant to process material up top of the quarry.
While nationally, the recession has hit some metropolitan areas harder than others, Mike and Perry agree that the Buffalo/Niagara area experiences less peaks and valleys and remains closer to the center of commercial and private development activity. The local air base, big box stores such as Target and Kohls and median range housing developments with some high end subdivisions in areas such as Lancaster, a suburb east of Buffalo, continue to contribute to modest growth.
Bob Turner, Lippmann’s president stated “While we’ve built our reputation for designing and manufacturing highly reliable, productive products, outstanding customer support, is how we continue to grow our company. For all of our customers, like Catco and Lafarge, we are committed to the continued success of their business, throughout all economic cycles. Recently, we have experienced a very strong upturn in equipment demand and trust it will continue.”